What it takes to get goalposts ready to go to work

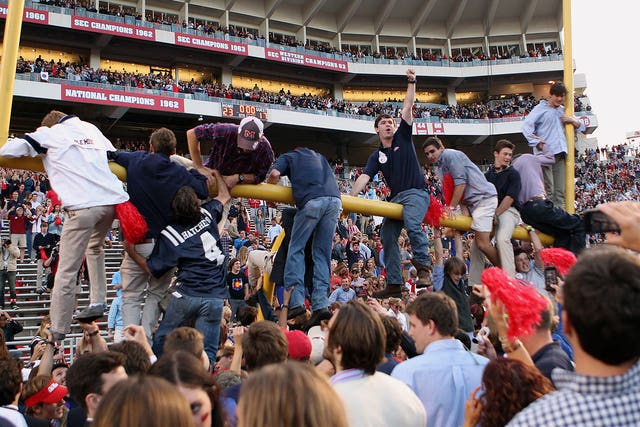
Last year in the NFL, 35 different kickers made a total of 1,262 extra points and 863 field goals over the course of the regular season, and chances are good that not once did any of them — or any of us watching — think twice about the goalposts those kicks sailed through.
For David Moxley, however, goalposts are pretty much always on the brain. As the director of sports construction sales for Sportsfield Specialties, Moxley’s job, in part, is to make sure the goalposts his company manufactures are doing exactly what they’re designed to do: stand up straight, hold up to the elements and only get in the way when they’re supposed to.
From high school to college to the pros, goalposts are largely taken for granted — overlooked like other critical field components such as hash-marks and pylons — but the process by which the posts are made is quite sophisticated.
At Sportsfield Specialties, about 40 employees on the metal production team in Delhi, N.Y., create 400 to 450 sets of goalposts per year, with each goalpost requiring 15 to 18 hours of labor before it’s field-ready, once all the engineering, cutting, rolling, milling, welding and painting is finished. (The company also has a facility in Salisbury, N.C., where “soft goods,” such as goalpost padding, are made.)
With goalposts in 23 of the 31 NFL stadiums and countless college stadiums, Moxley and his colleagues know that precision is key and that there’s no margin for error — it would be front-page news for all the wrong reasons if a goalpost failed during a game, for example — but the operation leaves plenty of room for imperfection if instruments aren’t programmed and calibrated correctly and employees aren’t totally focused on the task at hand.
A standard goalpost is made up of four basic components: a base, called the “gooseneck,” a crossbar and two uprights. The gooseneck and crossbar at Sportsfield Specialties are made of dense schedule 40 aluminum, while the uprights are made of a lighter 1/8-inch wall aluminum. When built, a goalpost, which is secured into the foundation using either a ground sleeve or a base plate depending on the stadium, should be able to withstand winds up to 115 miles per hour, and is tested by an outside team of engineers to ensure its compliance.
“The uprights would be very heavy if you (used schedule 40 aluminum),” Moxley said, noting that each NFL goalpost weighs roughly 500 pounds even with the lighter material for the uprights. “The heavier stuff you put on top, the heavier it’s got to be at the bottom, so you’re looking for the lightest material possible that’ll still pass all the engineering criteria.”
Each component comes to Sportsfield in the form of a straight, extruded pipe. From there, the piece that will become the gooseneck is cut to the correct length using an industrial saw and fed into a machine to be bent to the proper size. Standard NFL goalposts have a 6-foot offset, but some fields — primarily those that double as soccer fields — use posts with an 8-foot offset, so an entire goal can fit underneath the crossbar without running into the base.
To bend the pipe, two heavy, computer-controlled rollers are used to manipulate the straight pipe into the particular shape inputted into the machine. Once that process is finished, the gooseneck and the other pieces, which are also cut to size, go through several steps of milling and welding, attaching joints and other components to prepare them for installation.
“Let’s call it 50-50,” Moxley said of the split between the amount of work done by hand as opposed to by machine. “Because, while the machine is doing the bending and the drilling, you then have people who are doing the welding, and the cleaning of the product, getting it all ready to go to paint, and the paint process — even though the paint is the product that goes on, it’s very much about how you apply it. And not only that, but the machines wouldn’t be able to do what they do if people weren’t programming them.”
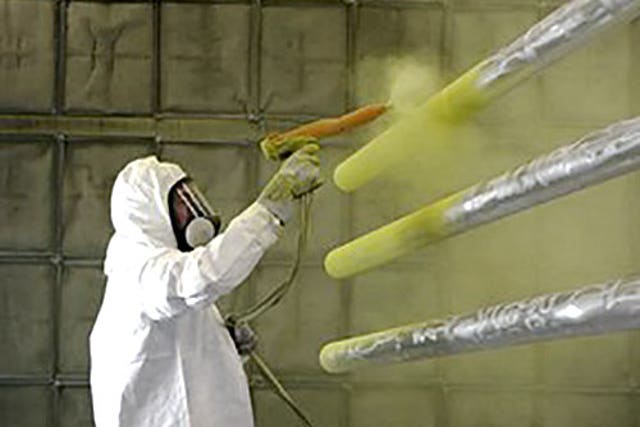
The painting process is underway.
After the welding is complete and the components are physically ready to go, they are painted using a technique called powder coating, in which a dry outer layer is applied using a tool called an electrostatic spray gun, then heated to cure the paint. Typically, goalposts come in either yellow or white. The NFL provides Sportsfield with two or three approved shades — essentially the same color, from different manufacturers — that can be used on their goalposts.
Once the painting is done, the components are shipped to the field to be installed, at which point the teams or schools can hire a contractor or installer to set them up, or they can just do it themselves.
The latter is one of the reasons Sportsfield uses aluminum in its goalposts as opposed to steel, which is still the metal of choice for some goalpost manufacturers. At many stadiums, the field is used for concerts and other events when football isn’t being played, so the ability to remove and replace the goalposts easily is crucial to the grounds crew.
“It’s lightweight and gives transportability options to the stadium,” Moxley said. “Steel is obviously much heavier and has much more corrosive properties, meaning if the paint fails or there are any paint issues, the steel is going to be much less forgiving than the aluminum. So really it’s from a weight and finish standpoint, and an aesthetic standpoint.”
All told, a set of goalposts costs between $7,000 and $14,000, depending on how many bells and whistles a team wants them to come with. (There are some that can be spun around in place, and others that can be raised and lowered using hydraulic pumps, for example.) And once installed, the shelf life of a goalpost can be as long as the team wants it to be, though they’re usually replaced about as often as when teams make other upgrades to the stadium or playing surface.
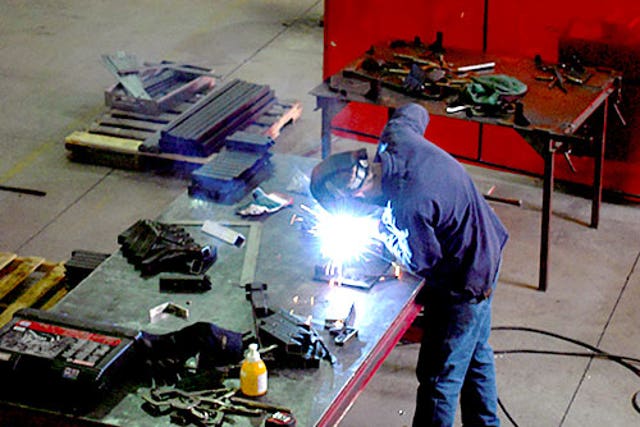
It takes 15-18 hours to get a goalpost finished.
“They probably last much longer than any of us would expect, minus the paint, which is always going to have some fade issues over time, and all of the things associated with mother nature that could hurt any product out in the field,” Moxley said. “So there is normal wear and tear, but as long as they can stand up to windload, they’re going to be fine for a very long time.”
Of course there are always exceptions to the rule, especially at the college level, where fans sometimes celebrate a monumental win by snapping the goalposts or ripping them right out of the ground — a practice that, while not advisable, is more difficult than you think.
“Like anything, if you put too much weight on it, it’s going to fall to the ground,” Moxley said. “The first concern is obviously everybody’s safety. We don’t want anyone climbing on anybody’s goalposts, for that matter, which I think is why the NCAA and NFL have all instituted fines if people access their field. But there’s probably not a great answer for (how easy they are to tear down). It’s going to vary by manufacturer and vary by material and foundation sizes, those types of things.”
And then sometimes, goalposts all get replaced en masse, like they did earlier this year, when Sportsfield had to craft all new goalposts for each of its NFL clients after the league voted to replace the standard 30-foot uprights with 35-foot uprights. The change was referred to as the “Tucker Rule” by some, as it was thought to be inspired by Justin Tucker’s controversial game-winning field goal in a 2012 meeting between the Ravens and Patriots.
The NFL passed the proposal to change the goalposts on March 26, and gave Sportsfield a completion date of Aug. 1, no easy task for Moxley and his team.
“It wasn’t as simple as just putting five more feet on an upright; you had to go and re-engineer everything,” Moxley said. “So that was not only a unique challenge, but it had to be done in a timely fashion to get it done by the NFL-imposed deadline. It was a scramble to go to the stadium, get the outside measurements, meet with people and come back and make custom goalposts in almost every case.”
But all the headache was certainly worth it for Moxley and Sportsfield Specialties, and after 600 extra points and 397 field goals through the first eight weeks of the 2014 season, the league’s most underappreciated, yet critical pieces are operating according to design.
“It’s a very interesting business, and it’s great,” Moxley said. “It’s sports, and sports are fun.”
You can follow Sam Gardner on Twitter or email him at samgardnerfox@gmail.com.
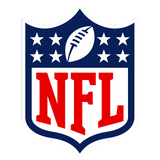